From Component Rebuilds to Complete Crane Systems
In 1980, G.W. Becker, Inc. was founded in Grove City, Pennsylvania. We didn’t begin as a crane builder. We started as a parts reseller and distributor. But before long, we were sourcing hoists and trolleys, fabricating girders, and rebuilding entire systems. It was gritty, hands-on work that laid the foundation for everything that followed.
By 1981, we had built our first pre-engineered packaged overhead crane and became an official ACCO Wright distributor. A year later, we introduced a line of custom brake wheels. We were solving customer problems before we even had a facility of our own.
Then in 1983, we moved to Division Street in Sharon, then again in 1986 to Dock Street. Every move reflected how fast we were growing. In 1989, we engineered two 40-ton capacity VAC transfer cars with four lifting beams. It was one of our earliest signs that we could do more than supply parts, we could build something that moved industry forward.
Finding Our Footing in Manufacturing
Starting in the 1990s, we were awarded distribution rights for Gorbel, adding even more to our packaged crane offerings.
Throughout the decade, we developed a reputation for being the company that could rebuild or re-engineer what others wouldn’t touch.
In 1995, we engineered a 2-ton TRSG Class C crane. By 1996, we had rebuilt both 10-ton and 25-ton TRDG Class D cranes with 80-foot spans. In 1997, we completed a 20-ton TRDG Class D hot metal duty crane rebuild and also delivered a new 20-ton TRDG Class C crane with a 35-foot span.
1998 was a big year for us. Some of the highlights included rebuilding a 10-ton TRDG Class D crane with a 55-foot span, delivering a new 12-ton TRDG with a special cantilevered hoist, and rebuilding a 40/15-ton TRDG Class E hot metal duty crane. We also rebuilt two 5-ton tram cars with 460-volt systems and automated travel and dump controls, and delivered both a 3-ton and 5-ton TRSG Class C crane. That year we also bought our Wheatland, Pennsylvania manufacturing facility, which meant we could handle more of the fabrication work ourselves.
The pace picked up even more in 1999. We delivered a 5-ton TRSG crane with elevated girder and end notches for extra hook height, four 8-ton fully automated top-running transfer and lift cranes for an automotive E-Coat line, and a 20-ton TRDG Class D hot metal duty crane running at 230 VDC. We also built a new 10-ton TRDG Class C crane, a 3-ton TRDG Class C crane, three 2-ton TRSG Class C cranes, and another 5-ton TRSG Class C crane.
Chris Becker had joined the company a few years earlier in 1995 as Sales Manager, helping guide us through this busy stretch and into bigger opportunities.
A Turning Point: Custom Cranes Growth in the 2000s
In 2000, we began designing and manufacturing our own overhead cranes and delivered a 20-ton TRDG Class D crane operating at 230 VDC. In 2001, we acquired L.M. Stevenson Co. in Grove City and became a distributor for Yale and Shawbox. These steps strengthened our in-house capabilities and expanded our reach. In 2005, we became members of AIST, followed by MHI in 2007. That same year, we were admitted to CMAA and relocated to our current facility on Kirila Road in Hermitage, where we began building our in-house engineering team.
We knew we were becoming a trusted solution when, in 2006, a metals manufacturer awarded us a contract to replace 14 cranes across their production facilities. That customer still partners with us today.
In 2008, Chris Becker became President and George Becker became CEO. We also added R&M to our distribution network and completed what was then our largest project, 104 cranes across three orders for a railcar manufacturing facility in Alabama. That job marked a turning point and proved we could successfully deliver at a national level.
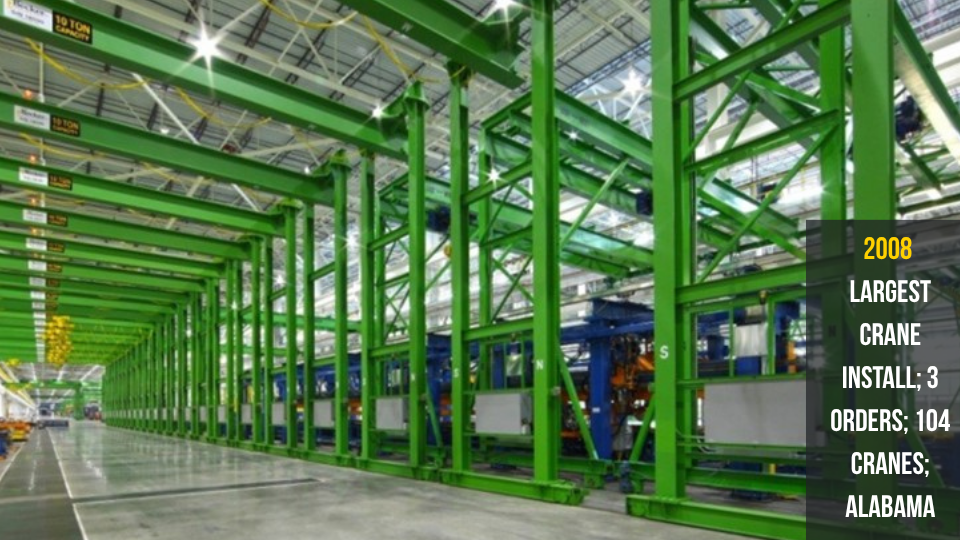
Expanding Reach and Capabilities
In 2010, we built a 15-ton twin-drop hoist crane for a pickle application and received the Phoenix Award for Growth from the Shenango Valley Chamber of Commerce. That same year, we were voted an Executive Member of CMAA.
In 2011, we delivered a 40-ton charging crane at 230 VDC and a 24-ton TRDG coil handling crane. In 2012, we earned our first Department of Defense contract, supplying eight cranes with PT runways to support the F-35 program in Oklahoma City. We also delivered a 25-ton charging crane with mill duty features.
In 2013, we delivered an outdoor 4-ton automated overhead crane and completed our first install in Mexico with seven cranes and runway systems.
By 2014, our automation and in-house engineering were at full strength. We delivered a 25-ton base-mounted hoist, a 1-ton automated parallel monorail system, a 20-ton TRDG heat treat crane, a 50/15-ton hazardous duty crane, and a 110-ton ladle crane. That same year, we delivered 51 cranes and 10 runways.
In 2015, we completed a twin 50-ton dredge bridge and leg structure.
2016 was filled with a lot of cool projects. We delivered a 25-ton stamping press crane, modified a 60-ton gantry crane, built a 6-ton dual hoist double girder crane with a custom spreader bar, delivered four 1-ton cranes, and engineered tandem 50/15-ton TRDG cranes. We also delivered a 20-ton heat treat crane, a 10-ton charging crane, and completed a 200-ton re-span project. We joined PNDC and received Gorbel’s Outstanding Dealer Award.
2017 was another milestone year. We acquired a sales and service facility on Broadway Road, won the Phoenix Award again, and earned an Economic Development Impact Award. We also completed a 31-crane, 16-runway project spanning 4060 feet, and delivered a 15-ton top-running double girder crane.
In 2018, we delivered a 50-ton TRDG crane, a 15-ton TRDG crane, a 2-ton crane, and more.
In 2019, we participated in the Shale Insight Conference in Pittsburgh and met President Donald Trump.
The Last Five Years: A Leap in Capability
2020–2024: Expanding in All Directions
As we entered the 2020s, we focused on expanding our in-house capabilities and meeting demand for higher-performance, more technically advanced crane systems. We started by investing in infrastructure and continued with specialized projects across the country.
In 2020, we completed a major addition to our Hermitage facility. This expansion gave us more space to scale our fabrication and assembly operations.
By 2021, production was really picking up. We delivered several new systems that year, including a 20-ton TRDG crane and two 15-ton TRDG cranes.
Then came 2022, which turned into a breakout year for complex builds and automation. We engineered and delivered a 60/20-ton Class F overhead crane running at 250 VDC, a 50-ton magnet duty coil handling crane, and an automated tube handling crane project. We also built a 25-ton TRDG crane with a 125-foot lift — one of the tallest lifts we’ve ever done.
In 2023, our automation work continued with a major delivery, an automated coil handling crane.
2024 has been one of our best years yet. The variety and scale of the systems we’ve delivered really show how far our team and capabilities have come. Some of our favorite builds from the past year are 40-ton hazardous environment overhead crane, 30-ton Class F slab handling cranes with rotating lifters, a 10-ton single girder crane, and both 5-ton and 10-ton single girder packaged cranes. We also delivered a 50/10-ton top-running double girder crane with rotating hook block, along with a 25-ton TRDG crane at 250 VDC Class F.
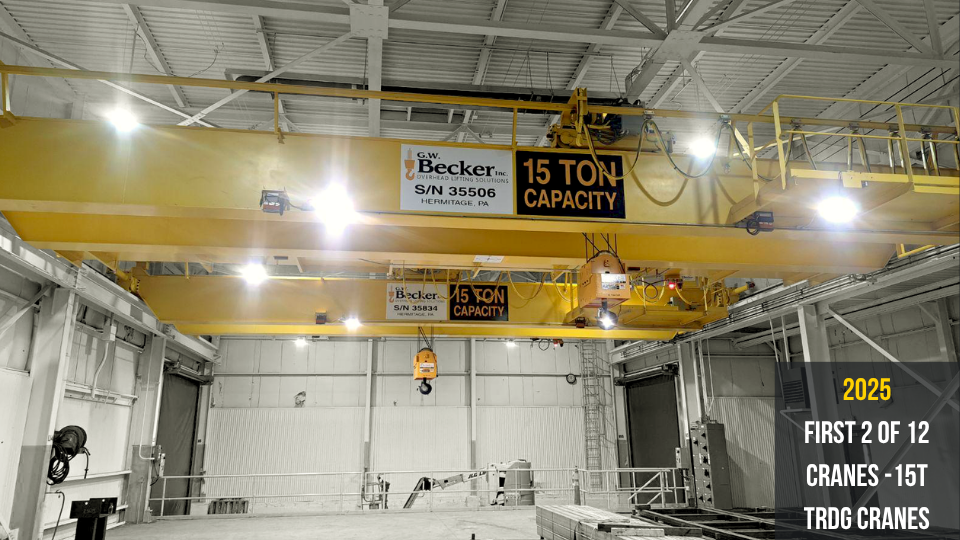
Investing in the Future
To keep pace with our growth and the complexity of today’s crane systems, we’ve continued investing in the tools and technologies that elevate our capabilities.
In 2024, we expanded our machine shop to support the growing demand for packaged cranes and hazardous environment systems. New additions included a CNC horizontal boring mill, a sub-arc gantry welder, and three advanced Mazak machines:
- SLANT TURN 600M: Handles hoist drums and drive shafts up to 36 inches in diameter and 160 inches long, with live tooling for precision and flexibility.
- MEGA TURN 900M: Ideal for large brake wheels, sheaves, and crane wheels up to 36 inches in diameter, with live tooling to reduce setup time.
- VC-Ez 20: Provides fast, accurate milling for bearing housings and small parts, supporting both custom and repeat packaged crane jobs.
These upgrades give us tighter quality control, faster turnaround, and greater in-house capability — especially valuable as we grow our packaged crane line and continue building rugged systems for harsh environments.
We also became a founding member of the Lawrence Mercer Manufacturers Coalition in 2024. This initiative supports local workforce development and reinforces our long-standing commitment to strengthening American manufacturing.
And to top off the year, a group of local students produced a video about our company that earned the Outstanding Creativity Award in the What’s So Cool About Manufacturing? contest. It was a proud moment for our team and a reminder of the inspiration that comes from sharing our story with the next generation.
Looking Ahead
Today, we can build nearly every component of a crane in-house, from engineered hazardous environment systems to efficient packaged cranes with shorter lead times. Our packaged line continues to grow, giving customers reliable solutions without the wait, while our hazardous duty cranes are designed to perform in the toughest industrial environments.
Our engineering team continues to expand in both size and technical depth, allowing us to serve a wide range of industries with confidence. What started as a small parts business has become a fully integrated crane manufacturing operation, serving customers in oil & gas, steel, defense, energy, automotive, aerospace, and general manufacturing.
We’ve come a long way in 45 years. And we’re just getting started.
Here’s to the next 45 years of lifting what matters.